Not Your Ordinary Engine Rebuild
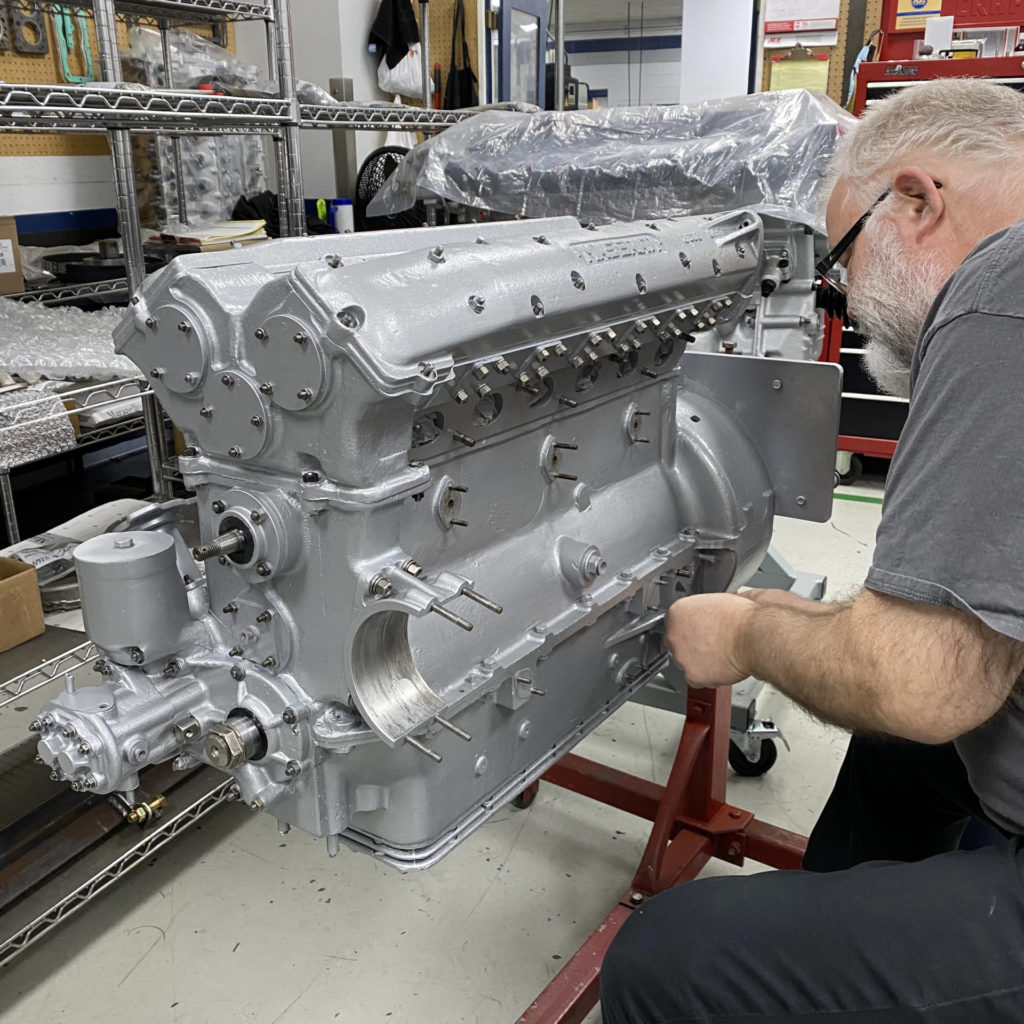
Rebuild, restore, reclaim. It’s our core discipline. In our engine department you’ll catch Mark Buhler, our master engine technician, reconditioning as many as ten different engines for our various restoration projects. Much of what Mark does is determine what is incorrect or broken, how and why it’s incorrect or broken, how to correctly fix the parts and components of the engine, and how to put back all the pieces to supply a strong, reliable engine.
Mark Buhler has been with Motion Products, Inc. for 15 plus years. He came in with 20 years of prior experience at a parts shop where he did various machining projects. At MPI some of his first projects were machining engine parts, then after a while he was introduced to the Italian engines. Since then, Mark has learned and grown his knowledge along the way to return engines to their authentic versions and performing as they should.
Building An Ongoing System that Works
Over time, Mark has developed a system that works for him and the rest of our restoration team to best get an engine back to its top performance making the rebuild process as smooth as possible. He has learned from one engine to the next, better ways to go about rebuilding an engine, and is continually learning to master his craft. In an interview, Mark shared his steps of the process.
First he prefers to have the car driven or tested on the chassis dyno to check for concerning sounds or vibrations. In addition to engine oil analysis, cylinder compression, and leakage testing, our test drivers can provide Mark with an impression of where they believe an issue might be originating from, giving Mark a good idea where to look for possible issues before he even dives into disassembly. This is of course, if the car runs and drives when we receive it.
Then our mechanical disassembly team will take the engine out and hand it over to Mark, sometimes with a test on the engine dyno first. Mark continues dismantling the engine; one of the most important steps of his process. He must carefully take apart the engine, all along the way photographing where parts are, taking meticulous notes, and measuring all the parts to make sure when he starts to put it all back together the parts are positioned correctly. He also evaluates the engine and observes any parts that may need to be fixed, replaced or made by our in-house engineering and machining department. Fun Fact: for engine rebuilds, Mark may have 20+ pages of notes to refer back to in his assembly stage.
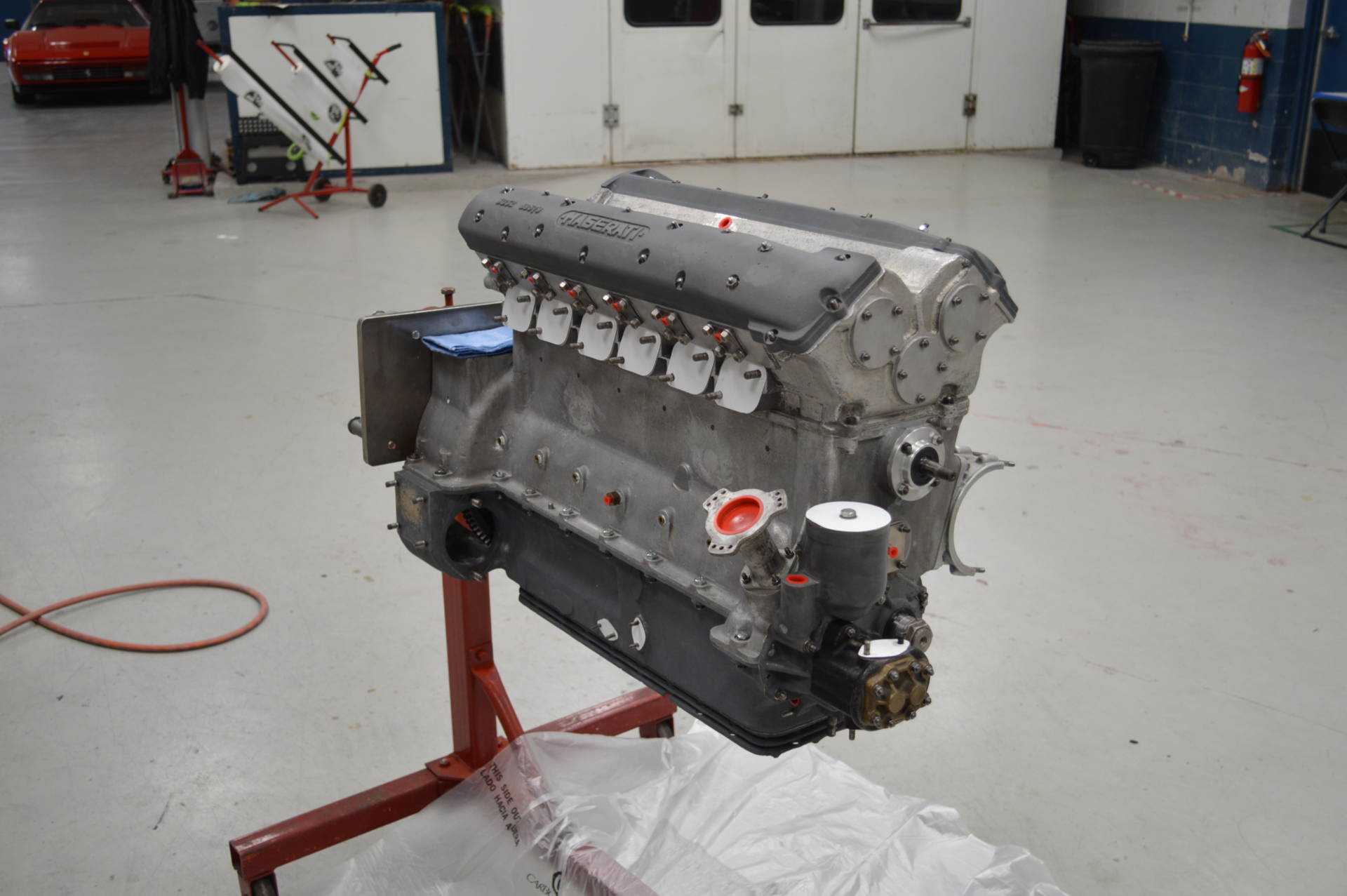
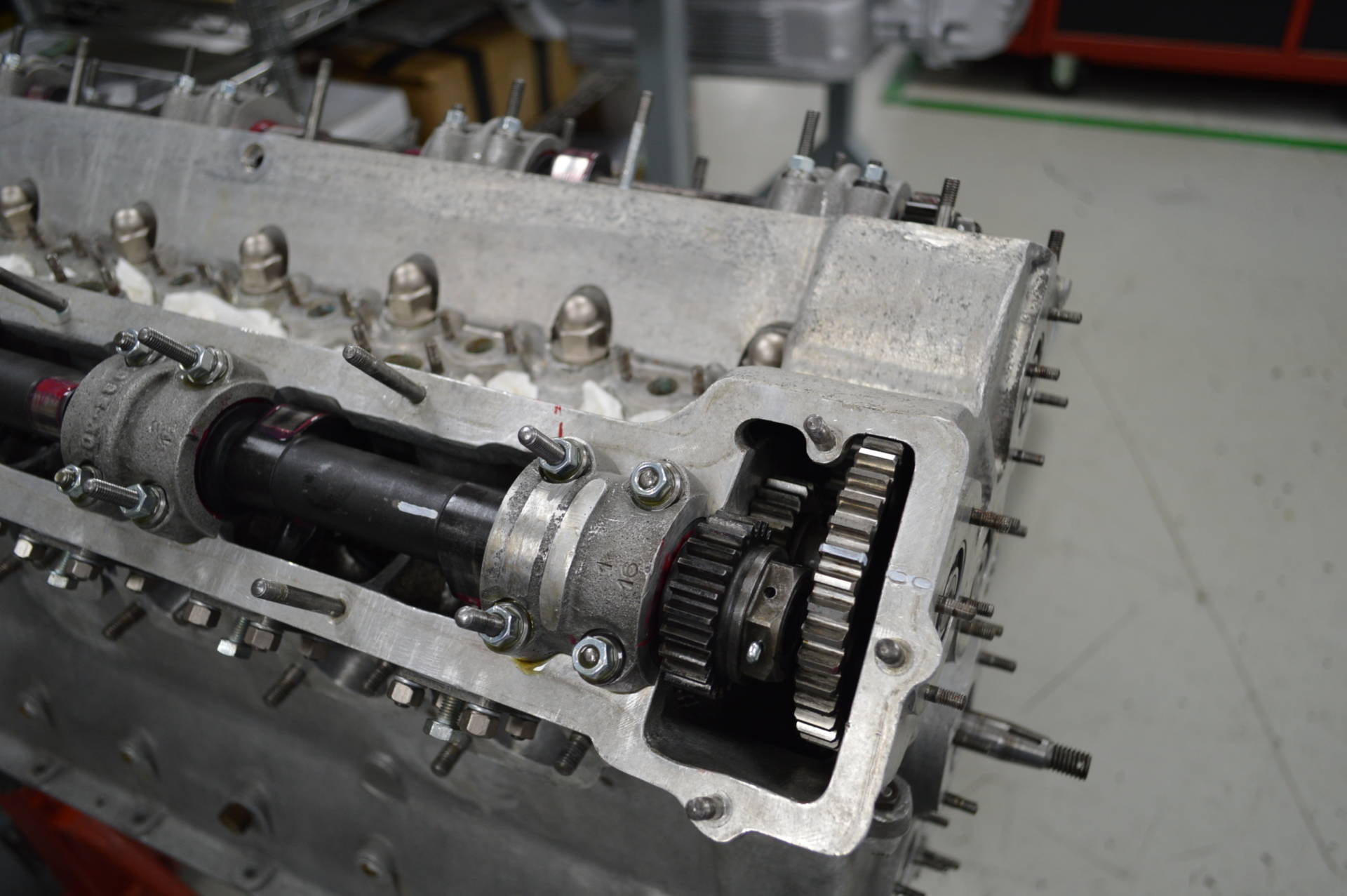
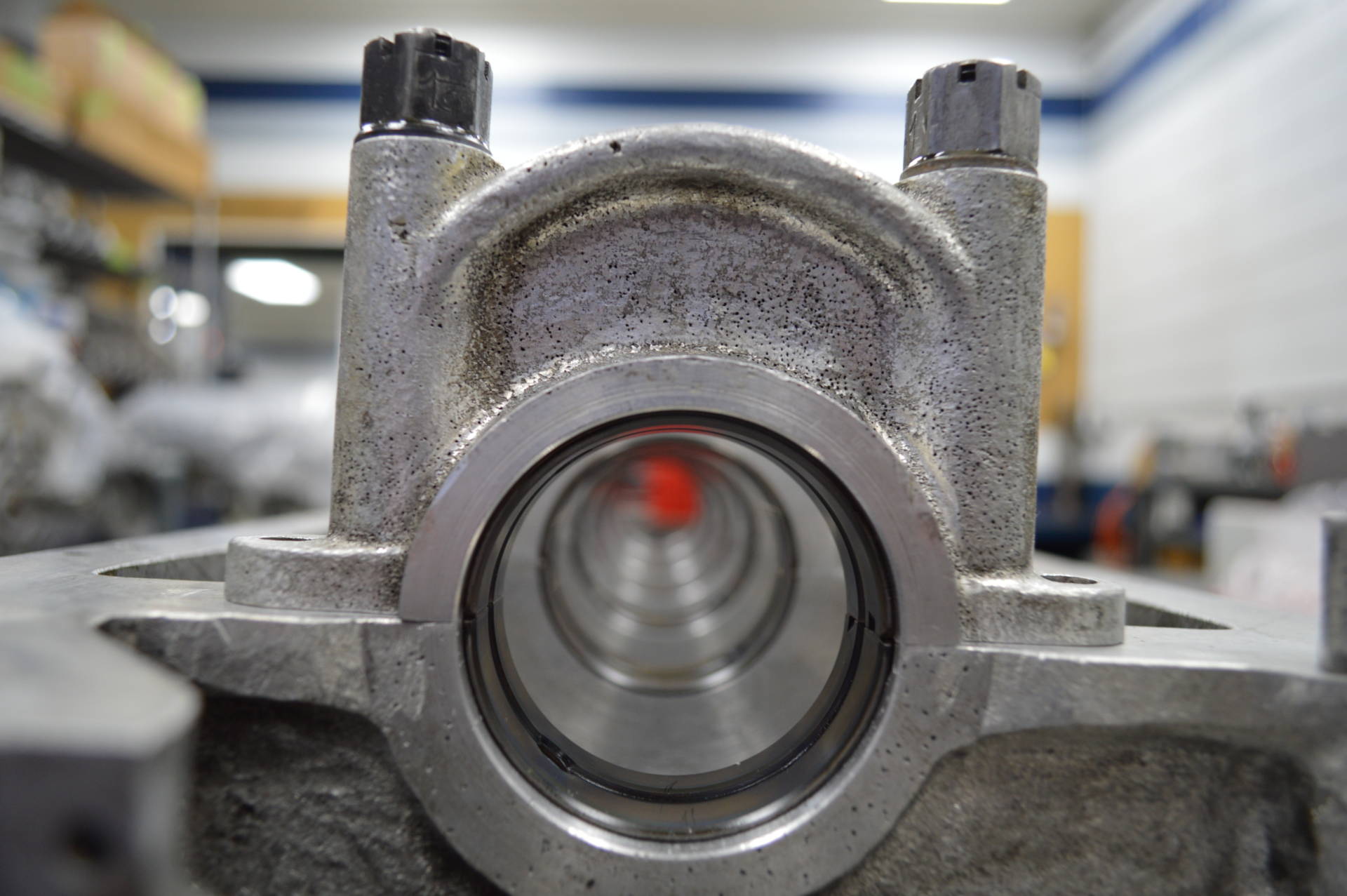
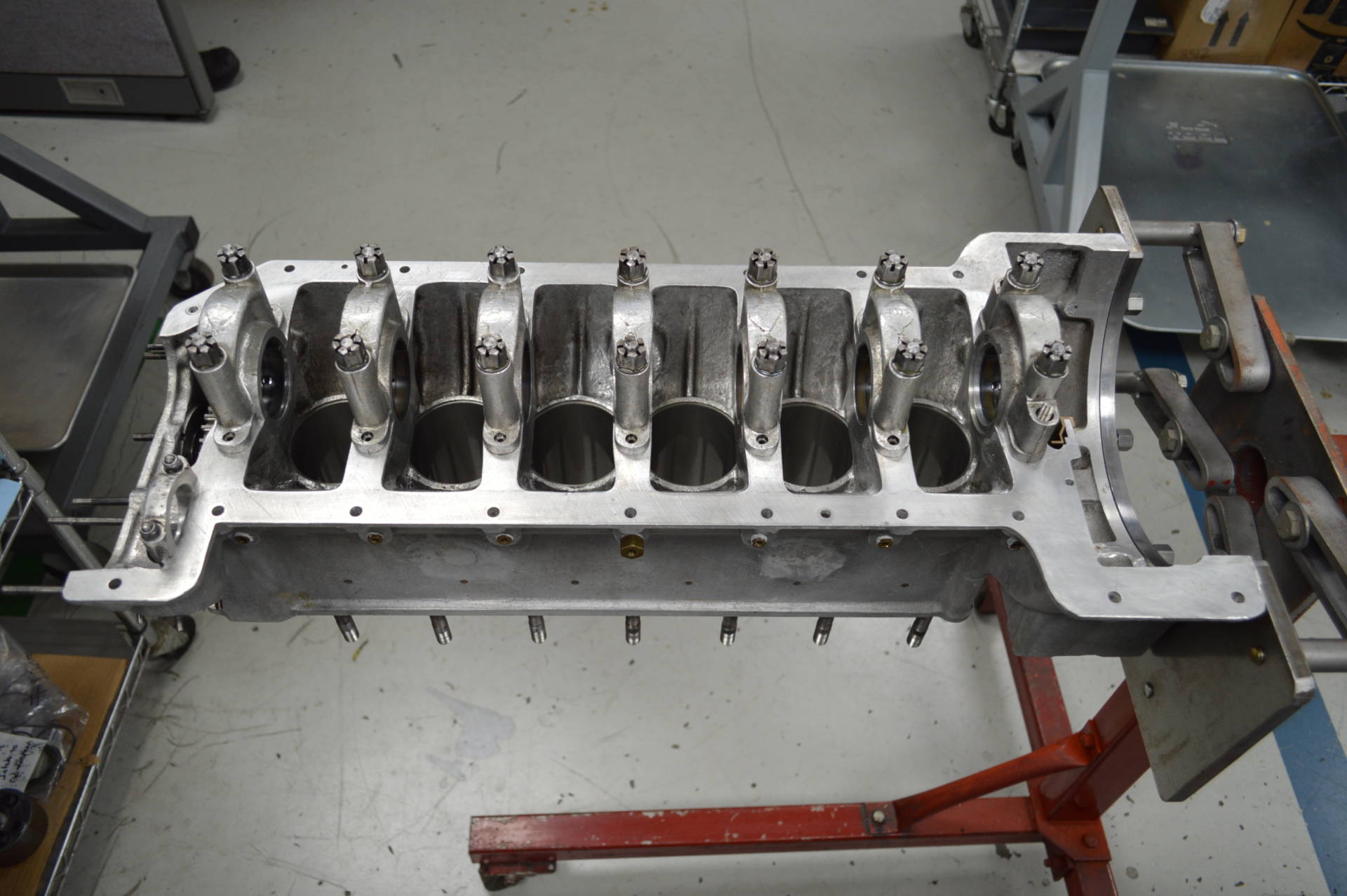
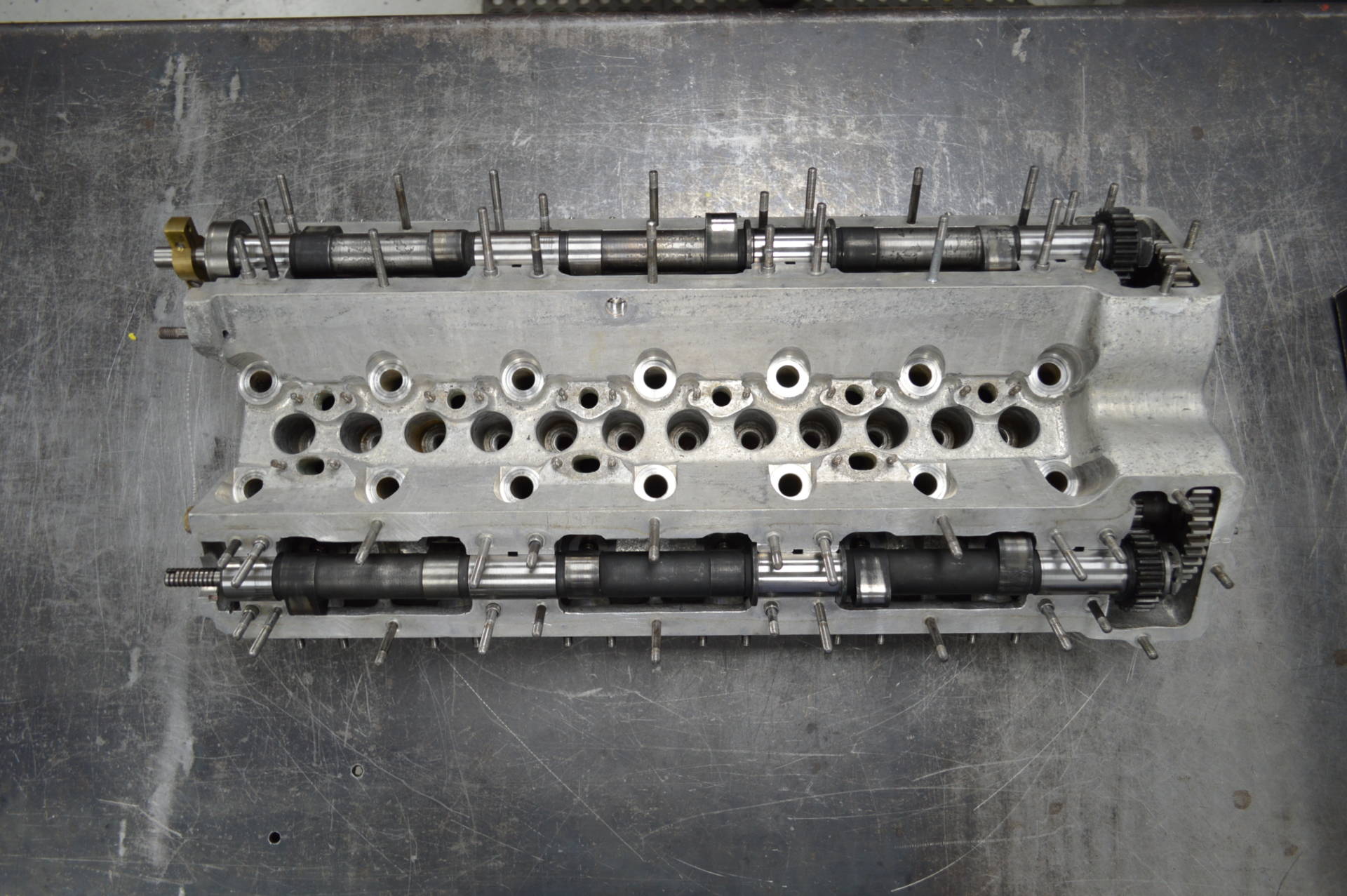
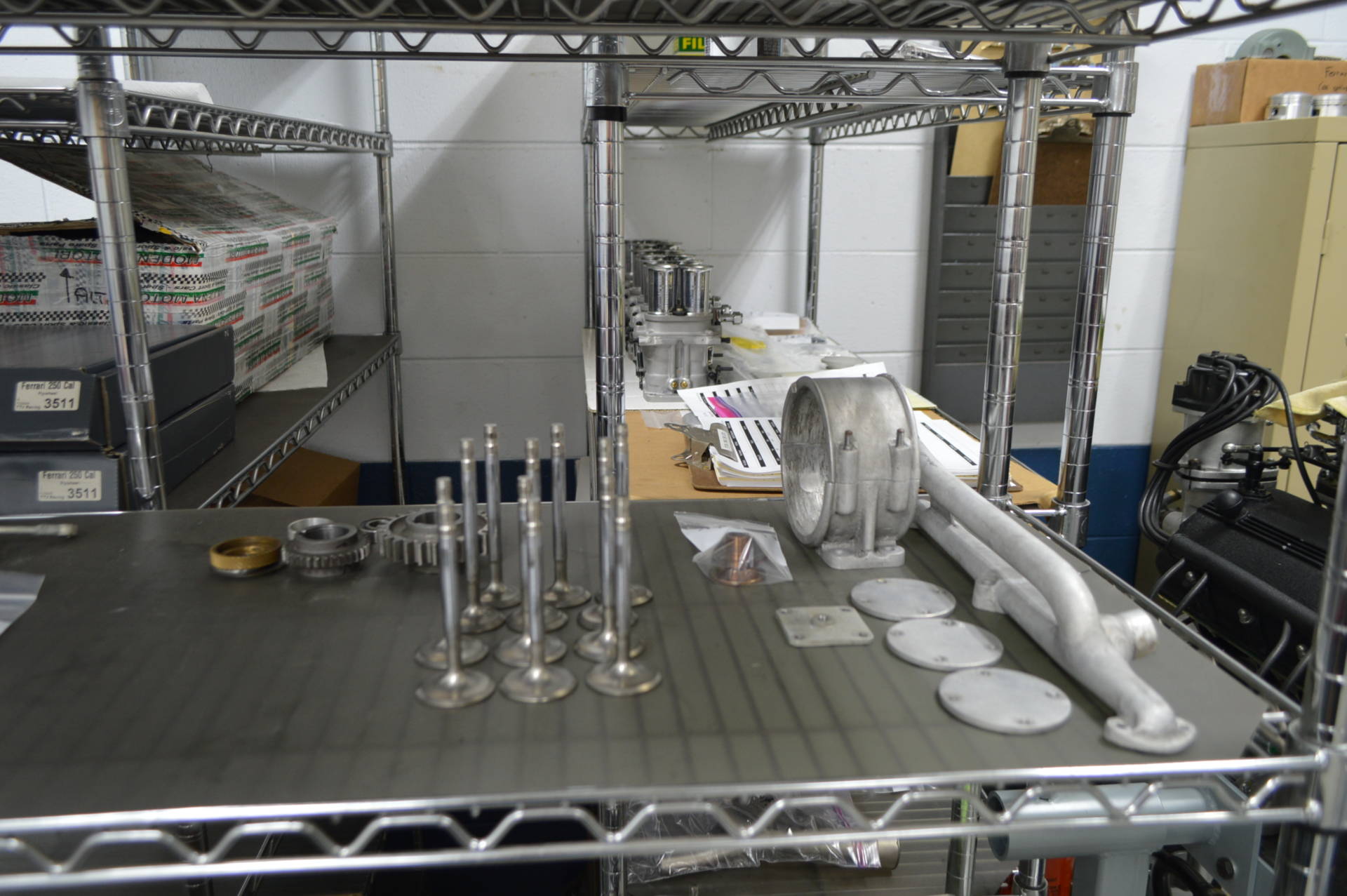
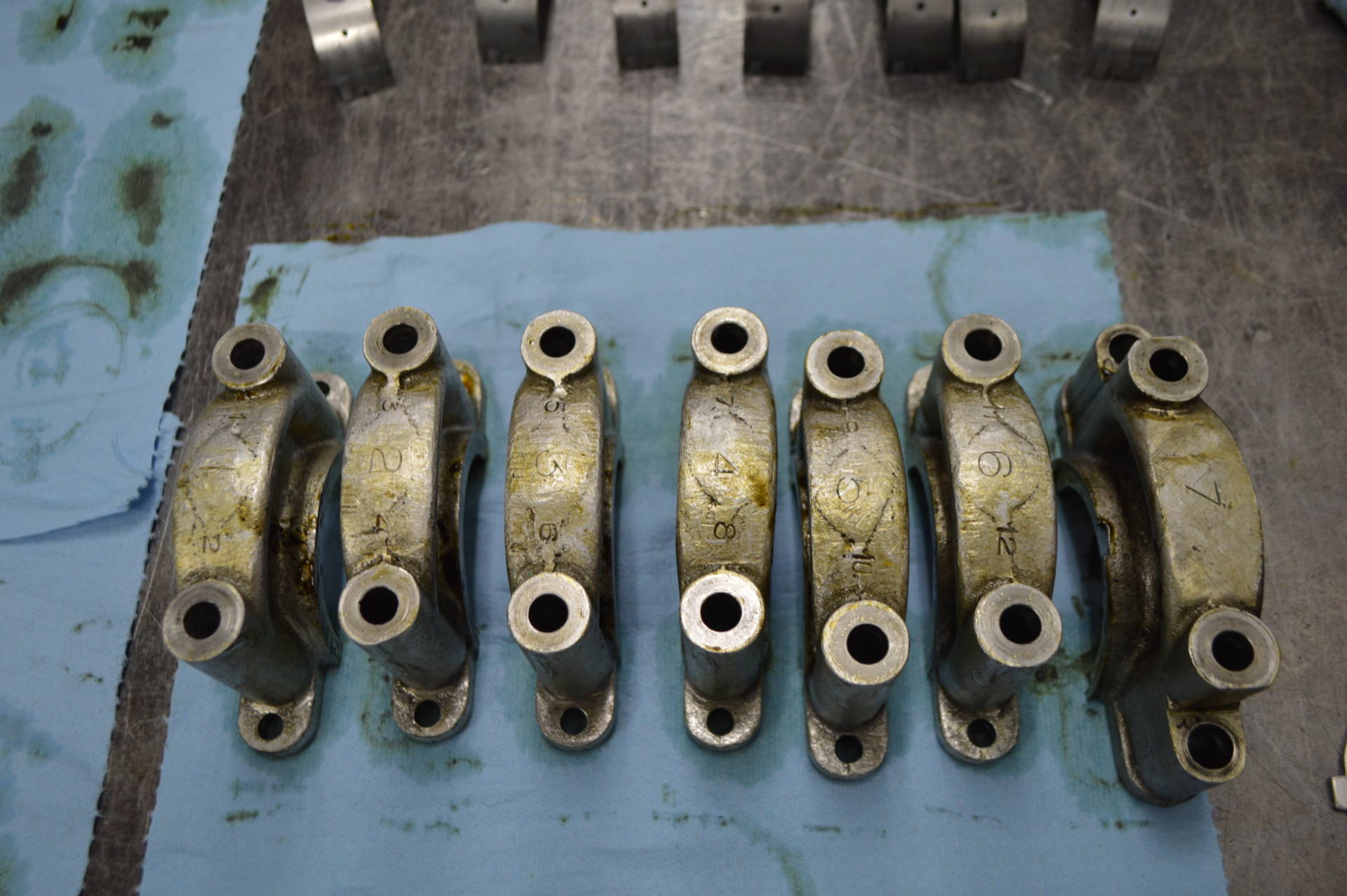
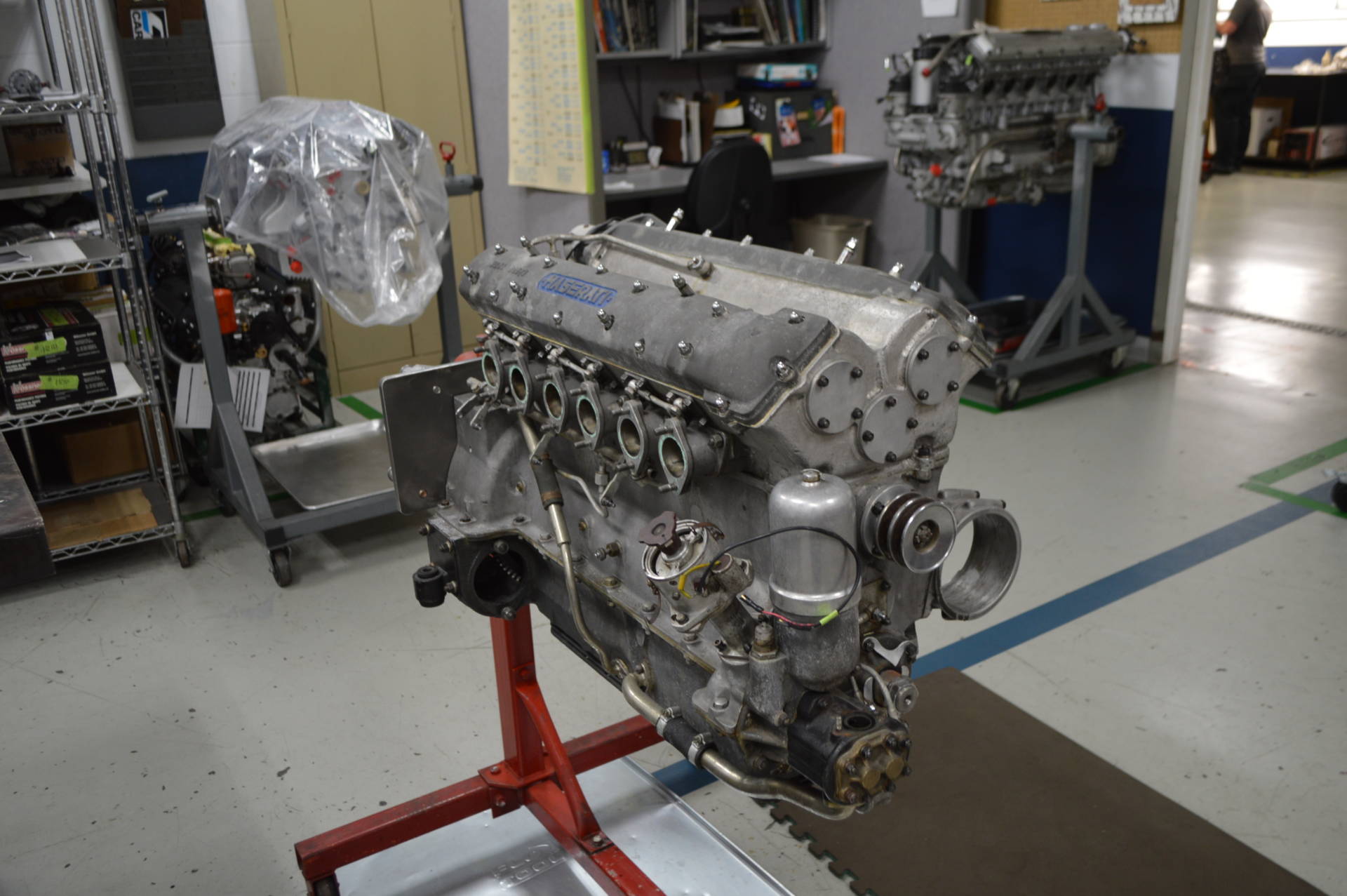
Right away, Mark will put together a list of what parts need to be replaced, fixed, or made to be able to complete the engine, and outline a plan if the project requires a lot of components to be repaired. The earlier our components and machining teams can assess replaceable parts, figure out a way to engineer them, or repair the parts, the sooner Mark can start reassembling the engine.
All of the parts and components make their way through our components department first for testing, correcting, repairing and a final cleaning before refinishing. Then our paint department will prep and paint any parts that need to be painted, or we send off any parts that need re-platted.
As Mark receives finished parts everything is labeled. Each engine has their own full wall-length shelf, and if you were to look down at an assembled engine from top to bottom, he organizes the parts in this corresponding order on the shelf. Once he has all the parts he does a final cleaning of the parts, and begins assembling the engine back together, piece by piece.
The assembled engine is then taken to the engine dyno for break in. This allows our team to check all the systems including the fuel system, ignition system, and checking for any possible leaks. Our dyno technicians also test the performance of the engine which involves some tuning. After the engine passes the engine dyno test, it’s reunited with the chassis.
Each engine rebuild will present its own unique challenges. Reliable repair data is rare and at times, outdated. In many cases, we must rely on experience, notes from past rebuilds and testing data to determine the proper course of action. “The major difference between domestic engines and European engines is that domestic engines were made to be simple, straightforward and to be mass produced. On the other hand these European engines were made for performance and results,” said Buhler. “I’m learning new ways to be more efficient rebuilding these engines all the time.”
Even though Mark primarily works on rebuilding engines, he enjoys seeing the before and after results of the physical appearance of the engine and how satisfying it is seeing the finished product comparing it to the initial oil covered, grimy engine. Within the full restoration, there are tons of little restoration projects going on, you just might have to look under the hood to uncover them.
Check out Our Team page for more information about our engine, engineering and machining, and components departments. And follow our social media accounts to see updates on the full restoration project of the Maserati A6GCS!
Leave a Reply